Special Thanks:
Thanks to all the people who provided excellent information on the Forum. This includes:
- Peter's (psfred) tips and safety advice
- csnow's tip on using the chisel to loosen the clamp
- 89-300ce's tips on tool selection
-
Shop Forum Thread
Disclaimer:
The following narrative describes how I worked on my car. This narrative must not be considered the best practices way to repair a car. The work I have performed on my car is purely as a hobby and I am by no measure a professional mechanic. My real job has nothing to do with the automobile industry and I am self-taught. The tools and techniques I use are clearly amateurish. Therefore, if you are planning on working on your car you must obtain the proper training, tools and components to do the job correctly. Many of the techniques I employ could be considered hazardous and would probably get a professional mechanic fired from a reputable facility. For example, the technique I use to restrain the suspension spring requires great care and conscientious maneuvering. I have heard that this spring can kill a person if it gets loose. And my technique has obviously nowhere near the level of safety-consciousness as the techniques prescribed by professionals. I TAKE NO RESPONSIBILITY FOR ANY INJURIES OR DAMAGE INCURRED BY RE-ENACTING OR FOLLOWING THIS NARRATIVE!
Warnings:
The suspension spring can kill a person if it gets loose. The technique I used does not provide adequate protection from this happening.
Brake dust is a hazardous material. I wore a respirator at all times and performed work in an open carport on a windy day. I also was extremely careful to avoid inhaling dust. This is not always easy when working with air tools in the wheel well.
Removing and replacing ball joints and tie rod ends requires extremely large amounts of force. These forces, in concert with an unsteadied suspension spring, provide a myriad of opportunities for a disaster on the scale of massive injury or death. I wore safety goggles at almost all times.
Do not knock back a few beers and attempt to do this! No kidding.

Greetings Earthlings
Now, where was I
Diagnosis
The prior owner told me the dealer recommended new ball joints. The front left wheel squeaked and made other strange noises that abated when I injected oil under the rubber boot on the ball joint. And considering the car has 190,000 miles I figured the ball joints needed replacement. I had also just done the tie rods on my wagon and found it made a huge difference in the steering play so I decided to do them as well. The tie rods weren't desperately needed but I figured while I was in there I'd do them as well, and decided that I'd probably tear up the old ones anyways while getting the steering knuckle off.
Next Time
If I were to do this job again I would have obtained a different ball joint press. The one I used was $60 from Harbor Freight and caused considerable frustration. My struts were in good shape and so were my brakes. Since they needed to be removed in order to get to the ball joints I would have replaced them if there were any doubt. Looking back I would have ordered the ball joints well in advance and then ordered a ball joint press based on the measurements of the ball joints. Modifying the press took a considerable amount of time.
Necessities
- A solid, concrete place to work on the car
- Wheel chocks
- A solid, reliable floor jack
- Respirator for brake dust
- Goggles, face shield
- Latex gloves (lots)
- Knee pads (knees dislike concrete after a few hours)
- Medium ball peen hammer
- 22mm 12-point box end wrench
- 7mm Allen wrench (unusual size)
- Fat Chisel (big screwdriver might work)
- Pickle fork for removing tie rod ends
- Ball Joint Press (see note above)
- (2) Advil
- About 12 blocks of 4X4X12 wood
- A variety of thin pieces of wood
- Bench grinder to modify ball joint press and pickle fork
- Thick leather gloves
- A small amount of wax-like sealant that can endure moderately high temperatures. I used a sealant used by metal fabricators to keep out moisture. Caulking might have worked, but I'm not sure if it could withstand the temperature from the brakes.
- Metric torque wrench
- ½ Breaker bar
- Penetrating oil
- For degreasing I use a relatively safe, cheap solvent that used to clean brushes after painting. It is apparently safer and more effective than mineral spirits. I keep a plastic jar that is half-full of solvent and drop parts into it, put the cap on, and shake it for a bit. I lift the parts out with a magnetic rod. This is much preferable to spraying carb cleaner all over everything.
Glad I had
- Air Compressor
- Pneumatic hammer with attachment for pickle forks (makes getting the tie rods off a bit easier
- Impact gun
- 4 ½ angle grinder for modifying tools
- 4 vise
Parts
- Ball Joints
- Tie Rods
- New bolts from the dealer for the caliper, steering knuckle, ball joint clamp, etc (these are the front wheels we're talkin' bout!)
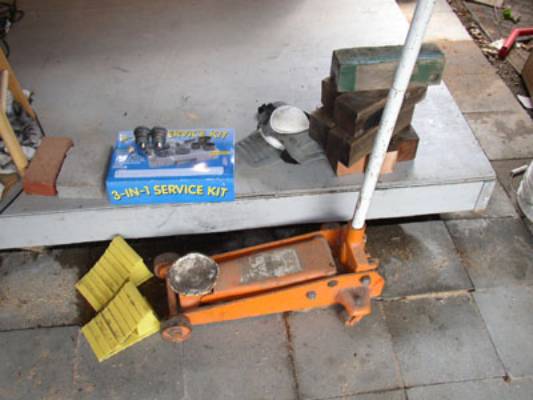
The Universal Ball Joint Kit (aka3-in-1 service kit) is from Harbor Freight. I guess MB is not from this universe.
I started out by placing wheel chocks on the back wheel on the opposite side the car that I was working on first. I did the driver's side first (USA) and chocked both sides of the rear passenger wheel. This was to prevent the car from moving either forwards or backwards. If the car were to shift midway through the repair the suspension spring could get free and take my head off. Wheel chocks, done. Parking brake, check.
Before jacking up the car I relaxed the lug nuts a quarter turn. I jacked up the car and placed 4X4 blocks beneath the frame. I gently lower the car onto the blocks, then pump the jack back up a bit so I know the car is supported by both the jack and the blocks.
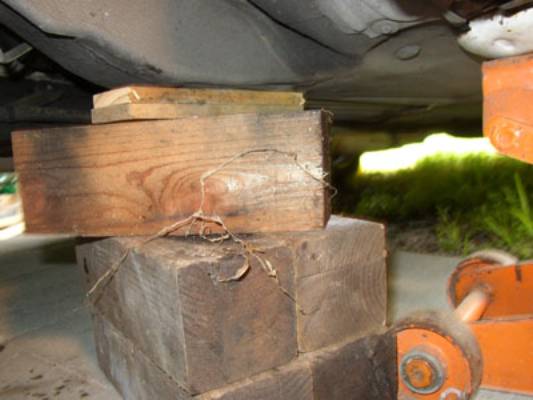
Next I removed the wheel and slid it under the car for a little insurance in case the car topples. I jacked the car up about another inch and then placed some blocks underneath the control arm. I made some mistakes here, but they were easily remedied. Basically if the blocks aren't placed just perfectly under the control arm, they will be in the way of the ball joint press later on. This is probably one of the many reasons why professional mechanics would use a spring compressor

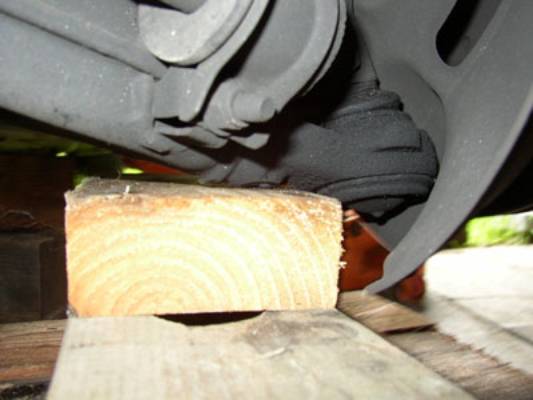
Close up look under the control arm. Notice all the grease on the old ball joint.
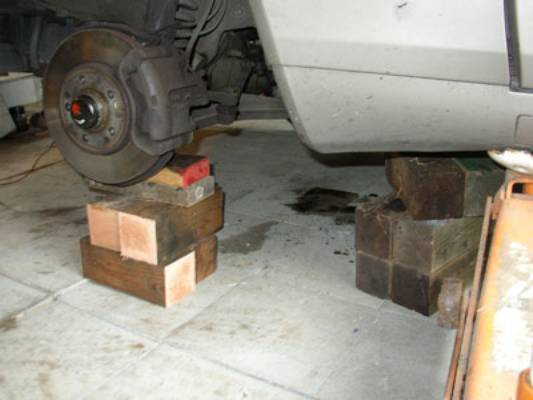
Notice the three places where there is support
This is how I first configured the blocks under the lower control arm. There was a problem with one of the blocks because it interfered with the ball joint press. Take a look farther down and you'll see how I should have configured them
Scary
The strut is what stops the spring from launching out when the car is jacked up. When the car is jacked up the spring pushes down on the lower control arm. The strut gets fully extended and then keeps the entire assembly together. If the top nut (near fuse box) of the strut is removed the control arm will very violently swing down and the spring will launch out with a vengeance and could literally take some poor fool's head off. If the bottom bolts of the strut are removed the control arm will very violently swing down and the spring will launch out with a vengeance and could literally take some poor fool's head off. The blocks supported the control arm so I could remove the strut. If the car had shifted, even slightly, the blocks under the control arm would have toppled and I would have been a poor headless fool. I was meticulous and conscientious.
Prior to removing the strut I slightly slacked all the nuts and bolts that needed to come out. This was to reduce the amount of force I would be putting into the car when the strut was removed. I removed the nuts for the tie rods and popped the ends out with the pickle fork, the pneumatic hammer, and a few well-timed swings of the ball pein hammer. I changed the angle on the pickle fork to make it more effective by grinding away some material with a bench grinder. This decreases the slope of pickle fork and provides more force to help pop-out the tie rod end.
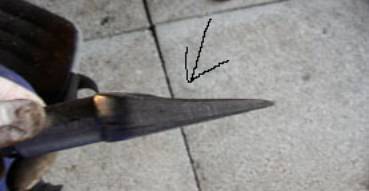
Modified pickle fork provides more upward force
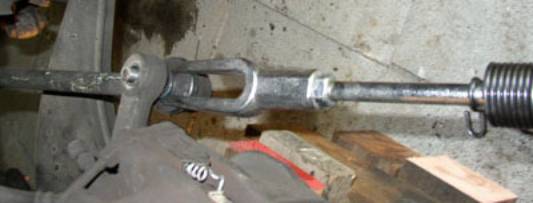
Using a pneumatic hammer with the pickle fork (and tapping on the stud with a ball peen hammer)
I removed the two 19mm bolts that attach the brake caliper to the knuckle and tucked the caliper in where tie rod connects to the steering box (this is to eliminate stress on the sensor wire or brake hose. I slacked the two 19mm bolts and the one 19mm nut/bolt that attach the bottom of the strut to the steering knuckle. There was no need to remove the steering arm from the steering knuckle. I removed 17mm rubber/bolt-like steering-stop thingy so I could get better access to the 19mm nut/bolt that clamps the steering knuckle to the ball joint. This required some patience and penetrating oil as it was very tightly bound up. I don't recommend slathering penetrating oil on all the bolts since the new ones come with a locking compound and I'd be concerned that residue in the threads from the oil would prevent the compound from doing its job.
I still hadn't removed the strut by this point for safety reasons.
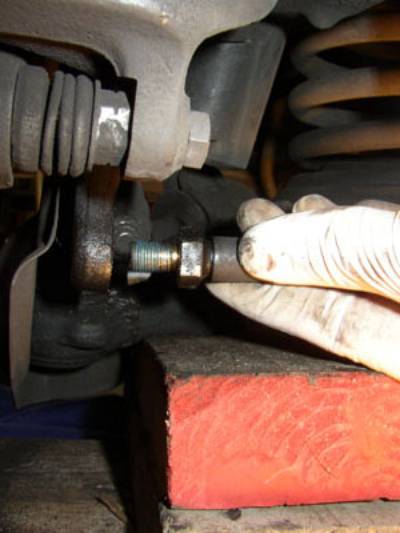
Removing the thingy
So at this point the three 19mm bolts that connect the strut to the steering knuckle have been loosened about ¼ turn. The 19mm nut/bolt that clamp the steering knuckle to the ball joint has been loosened a ¼ turn. The control arm and the chassis are both resting on blocks. The back wheel is chocked and the floor jack is also supporting the chassis. Three wheels are touching the ground. The brake caliper is tucked into the hole next to the steering box. I remove the Allen head bolt that keeps the brake disc attached to the hub and remove the disc. Since I wasn't removing the wheel bearings I didn't want to remove the hub, but the sheet metal was preventing the knuckle from sliding off the ball joint/control arm. Behind the hub there are three Allen head bolts that secure the sheet metal to the knuckle. I removed these three Allen head bolts. This gave the sheet metal enough room to clear the ball joint/control arm. I removed the two Allen bolts that secure the ABS sensor to the knuckle and tuck it away with the caliper. This is pretty fragile so I was careful not the bang it into anything,
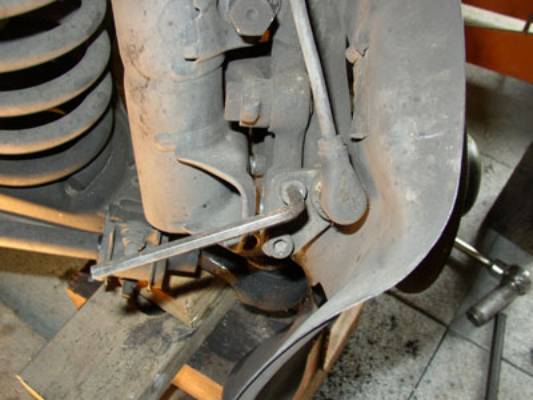
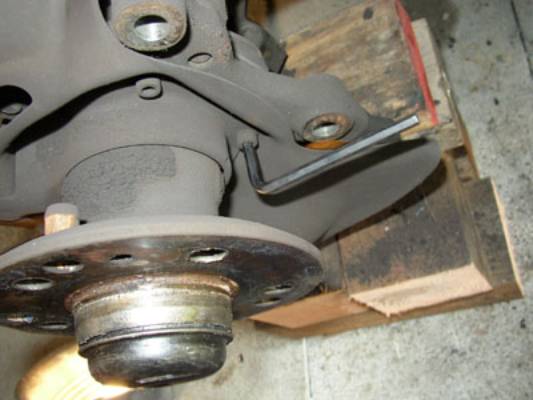

I now remove the 22mm nut from the top of the strut with the help of a 7mm Allen wrench.
I now completely remove the three 19mm bolts that connect the bottom of the strut to the steering knuckle. Next I pulled the strut up a little and fed it out past the front of the knuckle. I now remove the 19mm nut/bolt that clamp the steering knuckle to the ball joint. The factory seals the gap in the clamp with some wax. This will tap out easily. The bolt needs to be completely removed for the knuckle to slide up and off the shaft of the ball joint. I tapped a chisel into the clamp to spread it a little and dribbled some penetrating oil in there. That greatly facilitated getting the knuckle off.
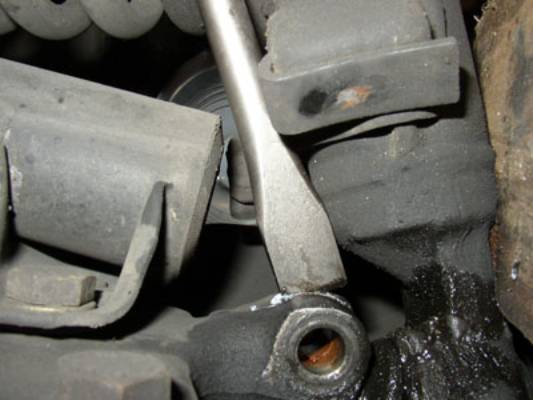
Using the chisel to loosen the clamp
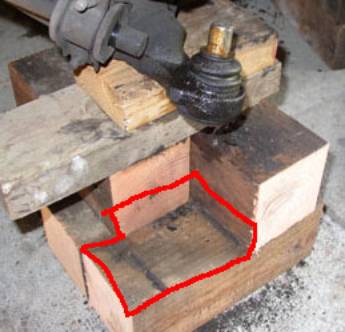
This is where the press needed to fit
Looking back, this is when I should have taken the Advil. The next step was pretty frustrating and I let the headache build until much later than was really necessary. (Unless of course there was some karmic debt that I was paying off)
Ball Joint Removal
The ball joint needs to be pressed down from above and it should pop out of the control arm. I tried pounding on the top of the ball joint at first, but it didn't budge at all. Since I've done some welding in the past I know how metal changes when it is heated. I've heard of people heating up ball joints to get to give it up but this seemed like a really really bad idea to me. The control arm is clearly a special grade of steel and there's not much meat around the ball joint. This means the metal is specially treated and would be weakened by heating. So there was no way I was going to take a torch to that area. I removed the 3-in-1 ball joint press from the box and attached it. It kept trying to slip off the control arm when I'd tighten down the screw. I took the 2 ¼ spacer that came with the press and ground down one edge with a bench grinder so it would seat better on the bottom of the control arm.
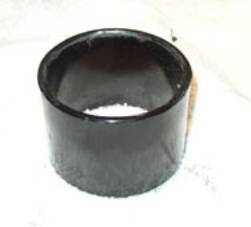
This is the spacer before I ground it down to work better
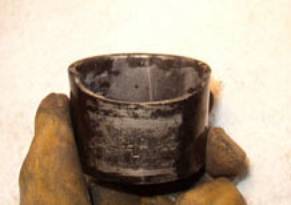
This is the spacer after I ground down one edge
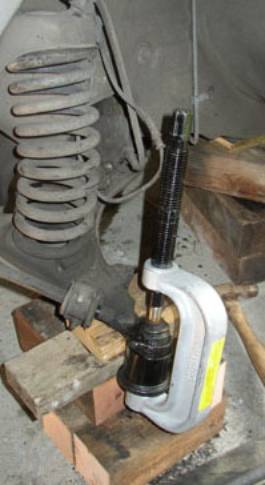
Looking good.

Oops.
Impact gun on top, and tapping away with a hammer on the press and finally it gave. Or so I thought. This is where things started to get interesting. The ball joint insert had punched-thru the bottom of the ball joint housing. The remainder of the ball joint housing was still firmly seated in the control arm. By trying a variety of spacers and re-rigging the press I was finally able to get the rest of it out. I couldn't handle the noise from the impact gun any longer so I balled up the corners of a lonely Mc Donald's napkin from the glove compartment and jammed them into my ears.
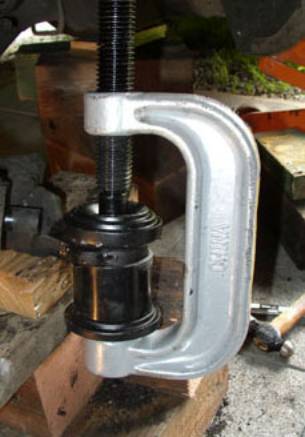
Configuration to push out the remainder of the ball joint
I think the impact gun makes things a little safer because a big wrench on the press could have torqued the car and disturbed the blocks under the control arm, thus letting the suspension spring fly away and go on a fool-killing spree
I cleaned the eye in the control arm where the new ball joint is going to live.
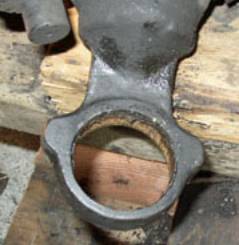
Ball joint is finally out
Ball Joint Installation
Since this is a Mercedes and nothing is similar with other cars, the ball joint press was not appropriate at all for pressing in the new ball joint. The press would have seated on the thin ball joint cap, and not on the high-strength rim that is meant to handle the force of getting pressed-in. So I took a piece of ¾ X ¾X5 steel stock that can be acquired at Orchard Supply Hardware. I ground down the stock so it would correctly interface with the seating rim of the ball joint. This took a while and the 4 ½ angle grinder made the job go faster and more accurately.
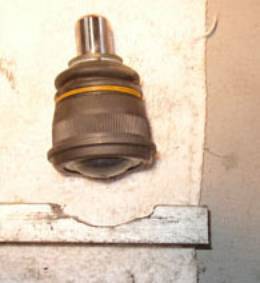
Steel stock ground to mate with ball joint edge and not touch thin metal cap
I took the smaller of the two spacers (looks like a piece of pipe) that come with the ball joint press and put that on the top of the control arm. I fed the ball joint into the eye, and was very careful to ensure that the notch in the ball joint rim lines up with the mark on the bottom of the control arm.
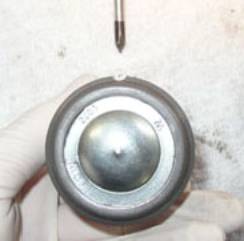
Then I put my specially formed steel bar beneath the ball joint and set up the ball joint press with a piece of angle iron on the top. I slowly tightened down the screw and occasionally shifted the position of the press to ensure the ball joint was going in evenly. It took a little while to get everything set up properly, but with a little patience and perseverance it finally got seated.
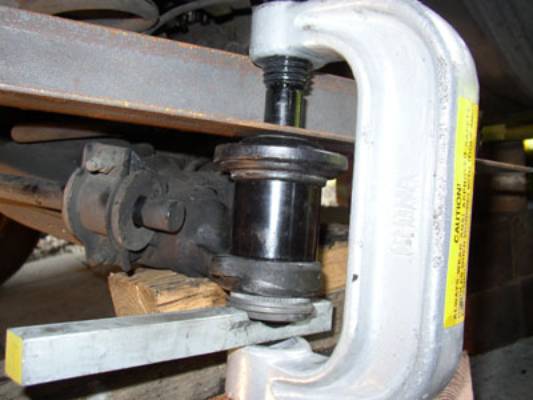
Not exactly how the Germans did it.
Prudence dictates replacing the 19mm nuts and bolts with new ones from the dealer. The new ones come with a special blue compound on the threads, and they are of a special grade of steel. After I seated the ball joint I cleaned up the threads in the steering knuckle so as to remove any residue and ensure the compound would do its job. Then I tapped the chisel into the groove of the clamp to ever-so-slightly spread it out a little.
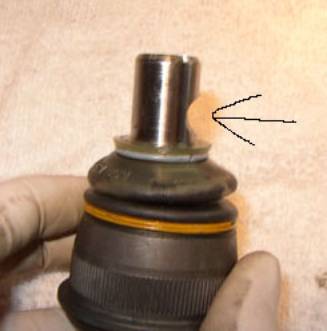
The clamp bolt passes through this notch
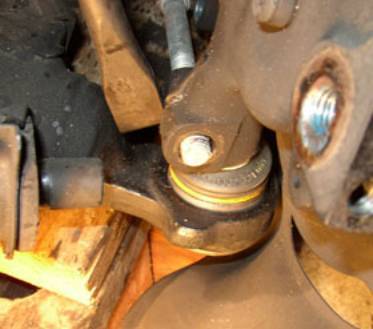
Using the chisel to help get the knuckle onto the new ball joint, and a scrap bolt to help align the notch in the shaft.
I examined the shaft of the ball joint to ensure the groove is on the inside. The bolt runs through the groove and everything must be perfectly aligned to get the bolt into its home. I then slid the steering knuckle onto the ball joint and used a scrap bolt to check the alignment of the groove. Since these are special bolts I didn't want to damage the threads by tapping it home. After I was satisfied with the alignment of the groove and the knuckle I put the new bolt in got the nut a little over hand tight. I wanted to get the strut back in place before torquing anything for safety reasons.
With the steering knuckle now on I replaced the strut exactly as I had removed it. I first got the 22mm top strut bolt started and then worked on the lower ones. This was for safety reasons. There's a little tit on the back of the steering knuckle that must perfectly interface with the bottom of the strut. I finger-tightened the two 19mm bolts and 19mm nut/bolt combo that secures the bottom of the strut to the steering knuckle. Then I torqued the top 22mm nut to 60NM. Apparently is very important to tighten 19mm nut/bolt BEFORE tightening the other two, shorter 19mm bolts. This is the one that goes through the strut and steering knuckle and sits horizontally. After this one was torqued I did the other two. . I think the spec on all these 19mm bolts ranges from 110NM to 125NM. Then I replaced the three Allen head bolts that secure the sheet metal to the knuckle, as well as the two Allen bolts to secure ABS sensor. I used loc-tite on these boltsThis where I used the sealant described in the necessities section to fill the gap in the clamp.
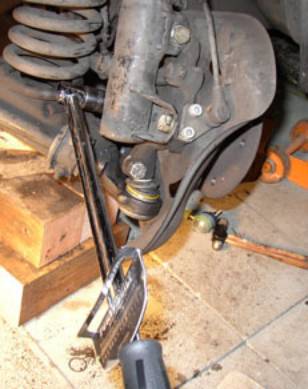
Top of the line torque wrench (that says 110NM)
I put some loc-tite on the 17mm steering-stop-thingy and put it back in its home. Afterwards I put the disc back on, as well as the Allen head bolt that affixes it to the hub.
Tie Rod Installation
In order to get the new tie rod within range I used a sliding clamp to get a measurement of the old tie rod. This got the alignment close enough to make it to the alignment shop. Installation of the new tie rod was a snap. Then I tightened down the two clamps that keep the tie rod from coming undone.
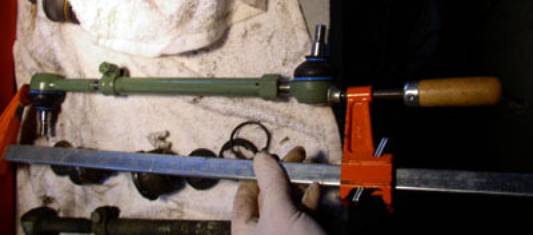
Using a bar clamp to approximate the length of the new tie rod
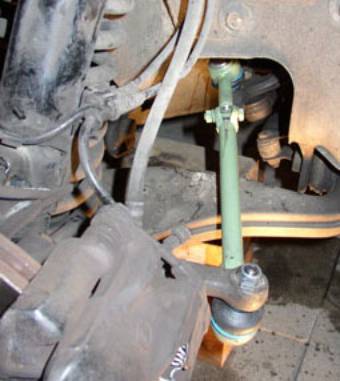
Installation of new tie rod left side (driver's side in the US)
I then spent a good amount of time making sure everything looked good. I re-examined everything, paying close attention to the top of the strut mounting and making sure everything was properly attached. After getting fully confident that everything thus far was properly assembled I jacked the car up so the control arm was no longer resting on the blocks. I replaced the wheel and got the lug nuts snug but not yet torqued. Then I removed all the blocks and lowered car. Then I torqued the lug nuts. The brakes needed a little pumping to reseat the pads. I backed the car up and over the chocks, as they were out of sight and out of mind. Oops.
Test Drive
I test drove the car and after a few miles it started making this incredible whining noise that was turning heads a full block away on a very busy street. I had been advised to be careful with the sheet metal that is attached to the steering knuckle. I had heeded this advice and was cautious with it, but had still managed to distort the metal. It was rubbing against the disc. I didn't need to remove the wheel, just formed it back into the correct position. I'm just glad I discovered this before my wife did.
Alignment
The car is now waiting to be taken in for a wheel alignment. I have found that the experience of the person performing a wheel alignment makes an enormous difference. I only take the car to an alignment guy who only does Mercedes. Suspension geometry is actually quite complex and varies considerably from model to model. Anybody who claims to have universal skills in wheel alignment probably uses universal tools. And we know from the ball joint press that Mercedes is not from this universe. Okay, that doesn't make a whole lot of sense, but just trust me on this one, I've had my E's aligned several times over the years and there's a huge difference.
Wheel Bearings
I should have cleaned out and repacked the wheel bearings prior to the alignment. I'm a believer in using the correct tool – a dial-in gauge – to set the wheel bearings. I don't have one of these tools and recognize that there's a certain amount of expertise needed to use it correctly. While the car was in getting the alignment I could have had the mechanic adjust the bearings. While the wheel is bolted on and off the ground, I grabbed it and vigorously shook it (but was careful not to topple the car off the jack!). There was a small bit of play so I tightened the axle nut a quarter turn. There's still a minute amount of play, but this will have to wait until I can repack the bearings and get the car back to my MB expert for adjustment. To clean out the bearings I time this activity to coincide with an oil change. A pan of hot oil dissolves out the grease nicely and everything goes to the recycler. A plastic spoon helps get out the grease. I let the hub drain out into the oil drain pan for a while and then hit it with some newspaper to mop up the residual oil.
What about the control arm bushings?
I considered doing the control arm bushings but realized that I would have needed to remove the spring and the anti-sway bar. This represented more than I wanted to do since a spring compressor would have been required. I believe the pro's remove the control arm and put it into a vice in order to replace the ball joints. If I ever come across a spring compressor I may do the bushings.
How long did it take?
Modifying the tools took a long time. The first wheel took about six hours, and in this time I experimented with a variety of ways to get out - and press in - the ball joint. The second wheel took less than three hours. If I had the correct press I imagine the entire job would have taken about six hours.
CategoryDiy