Front End Suspension Rebuild
on the 1982 300D (W123)
by bgkast
08/01/08
Note: This guide covers one side only. Both sides are identical, but use different upper control arms. From now on I will refer to the upper control arm as UCA and the lower control arm as LCA. The guide rod is also sometimes called the brake support. Be sure to use the correct type of spring compressor. If you are using a knock-off brand compressor you may need to enlarge the holes in the upper spring perches to fit the compressor down into the spring.
1) Disconnect the battery, place car securely on jack stands, and remove the front wheels.
2) Install spring compressor and compress spring
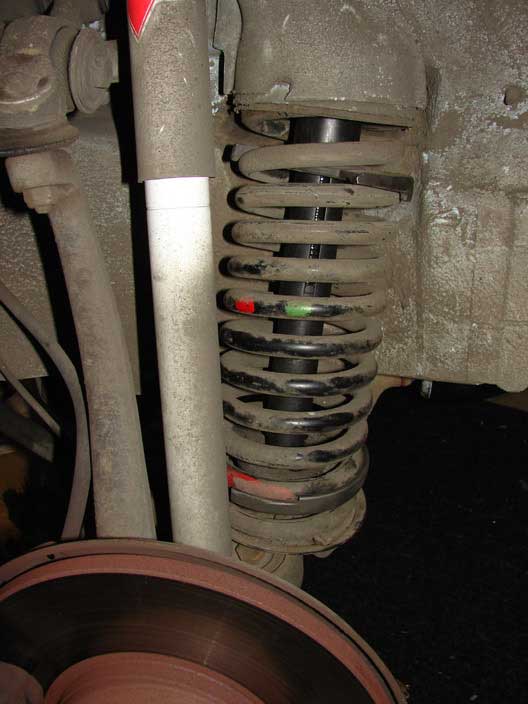
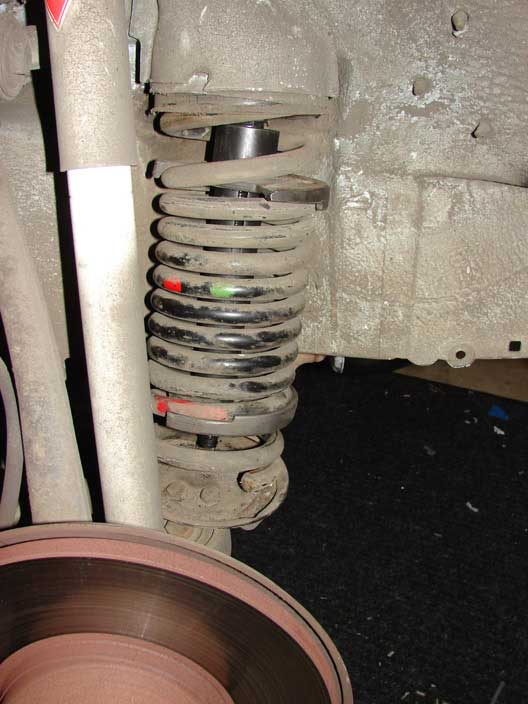
3) Remove spring from car.
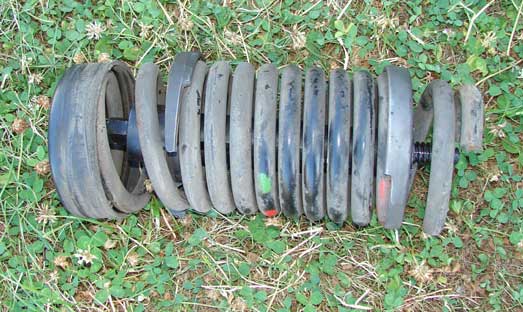
4) Remove Shock absorber and spring perch. I recommend threading the bolts that secure them back into the LCA so you don’t misplace them.
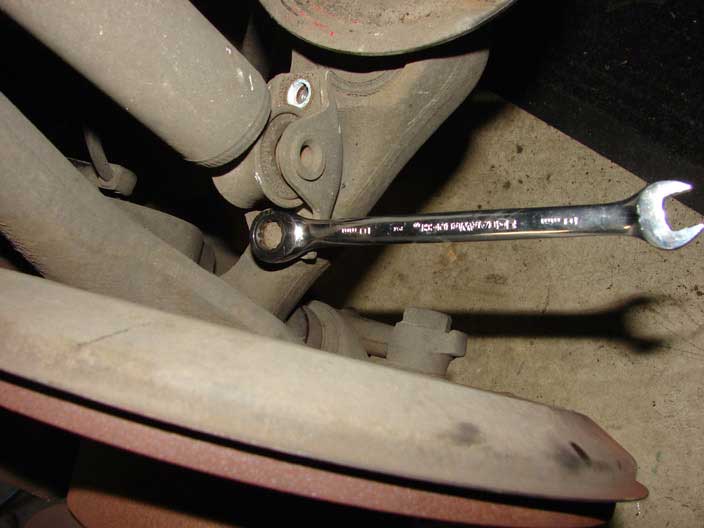
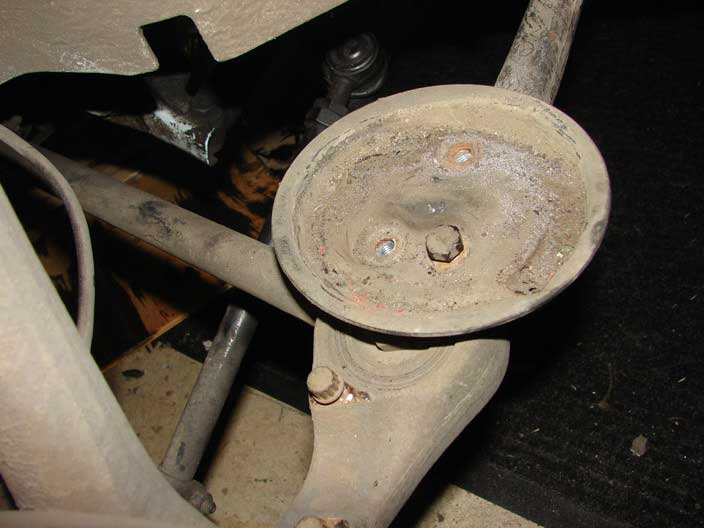
5) Remove three bolts that attach the guide rod mount to the body. Remove the bolt and bushing that attach the front of the guide rod to the LCA. Remove the guide rod (if you can finagle it out, otherwise wait until after step 6 to remove)
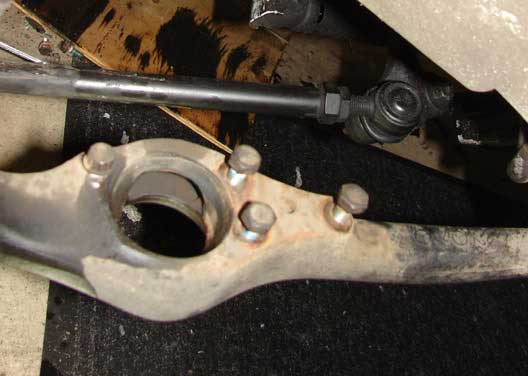
6) MARK THE ORIENTATION OF THE ECCENTRIC BOLT. Remove eccentric bolt nut and tap eccentric bolt out of LCA busing using a hammer. Use a rubber mallet to beat the LCA connection point free of the body mount. Remove the guide rod if you were not able to earlier.
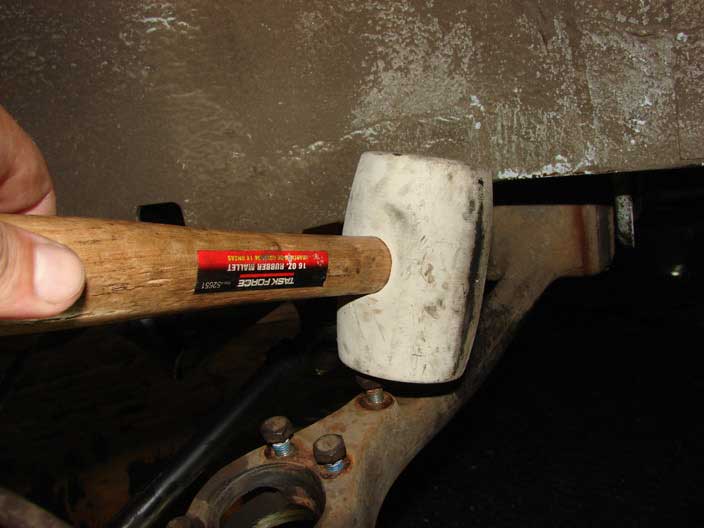
7) Use a sanding drum in a dremel to grind away the flair in the aluminum bushing in the LCA bushing. You don’t have to grind the whole flair, just grind a ring to separate it from the rest of the tube.

8) Remove the bushing from the LCA. I used a combination of prying with a screw driver and beating around the edges of the bushing with a rubber mallet to remove the two halves.
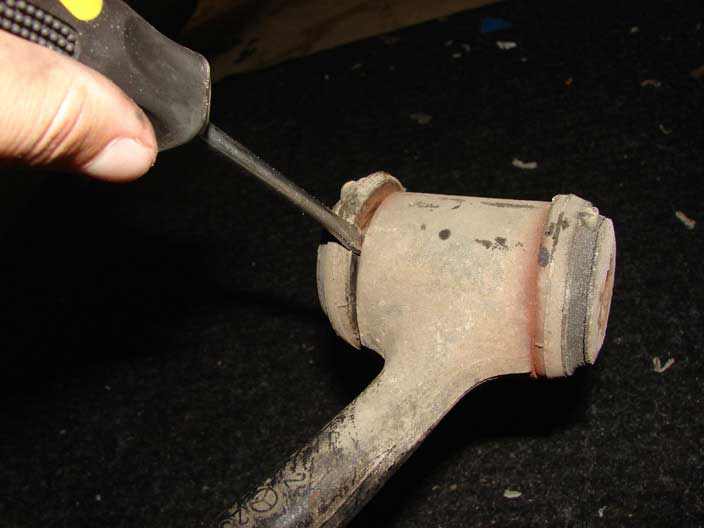
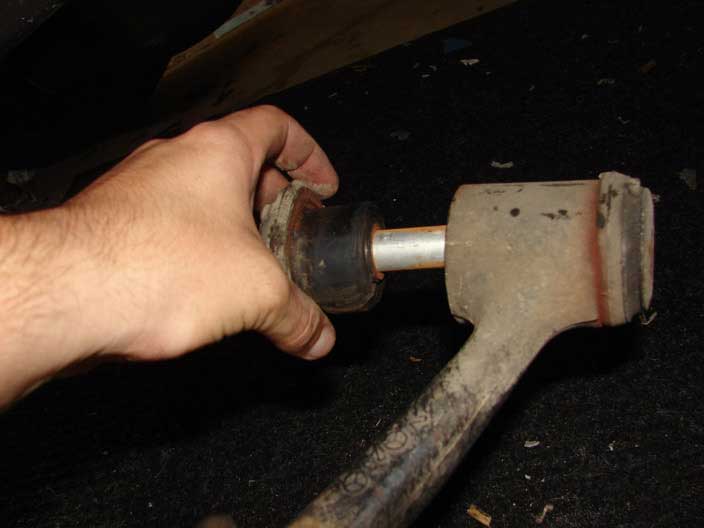
9) Clean up the inside of the LCA and coat with a rust preventative paint. I used Spray-Galv zinc paint.
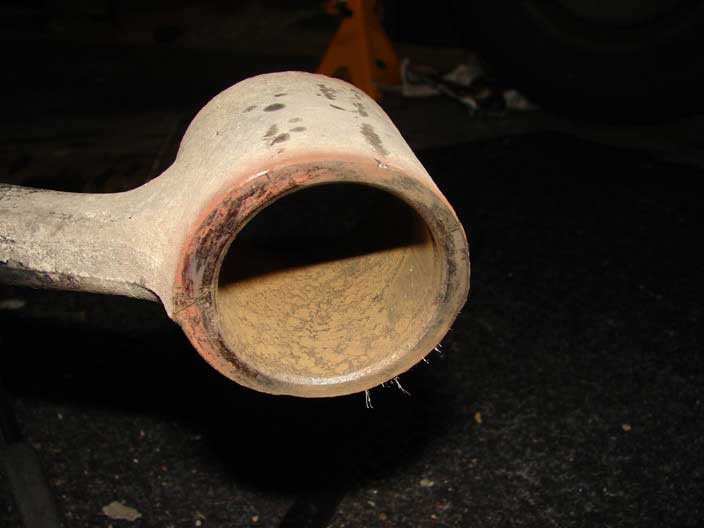

10) Place the new LCA bushings in the freezer for several hours to shrink them. When they are cold lube them with dish soap or KY jelly and press them in place with a vice. The flat sides of the bushings should be on the top and bottom of the LCA. BE SURE TO REMOVE THE NEW ALUMINUM TUBE BEFORE PRESSING THE BUSHINGS IN! (A stupid mistakes here will set you back a week while you wait for a new tube from Germany. Doh!)
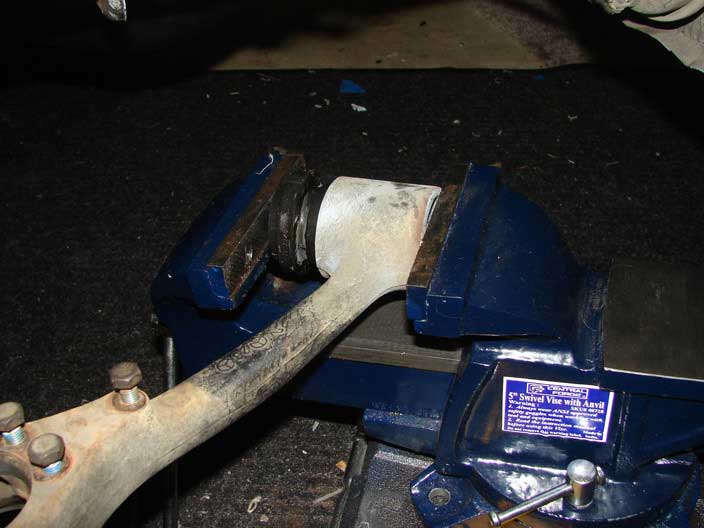
11) Install the aluminum bushing and flair the end. My first attempt at flaring the tube involved a 1/2" socket extension and my vice to squeeze it, however the back side of the tube got pressed away from being perfectly flush with the bushing while I was flaring it. When I tried to put the bushing in place the tube was damaged by the mount because it was slightly longer than the width of the mount. (That makes two flubs with this dang tube bushing). When my new tubes came in I made a tool out of a lug nut from my truck and a long bolt. This worked much better.
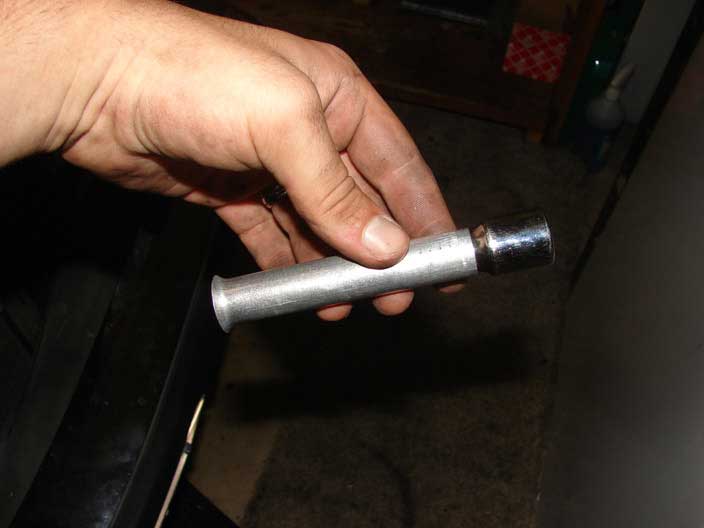
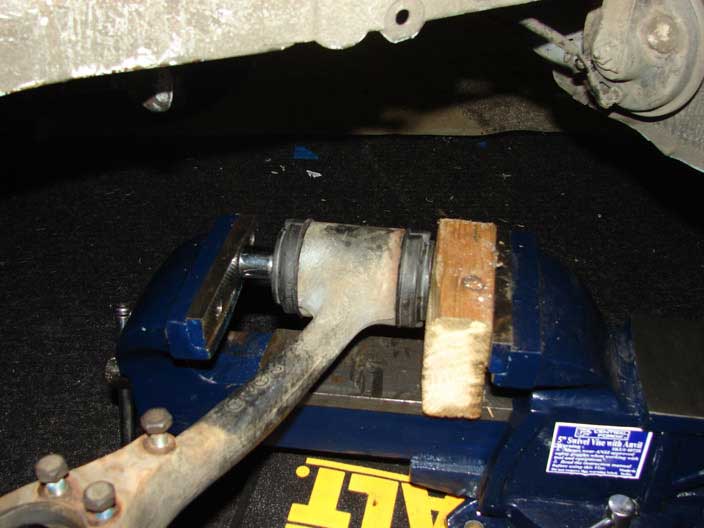

12) Install the new guide rod mount on to the guide rod. Before you remove the old mount take a 3' length of string with a washer tied on the end, thread it through the top mount hole and mark where the end of the guide rod falls.
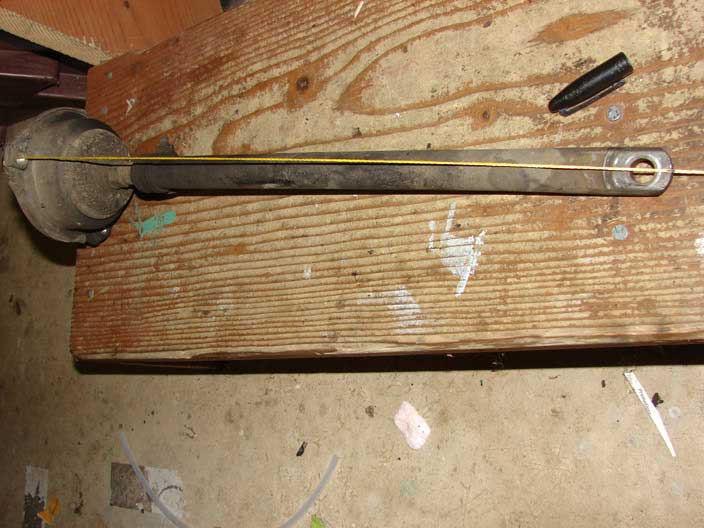
13) Loosen the clamping bolt, remove the old mount and install the new one. Thread the rod on to the mount until it is exactly the same length as before.
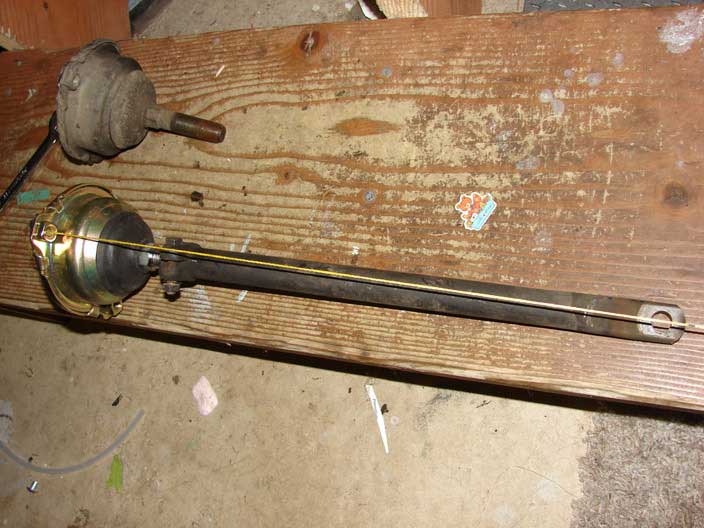
14) Reconnect the guide rod to the LCA loosely using a new bushing mount.
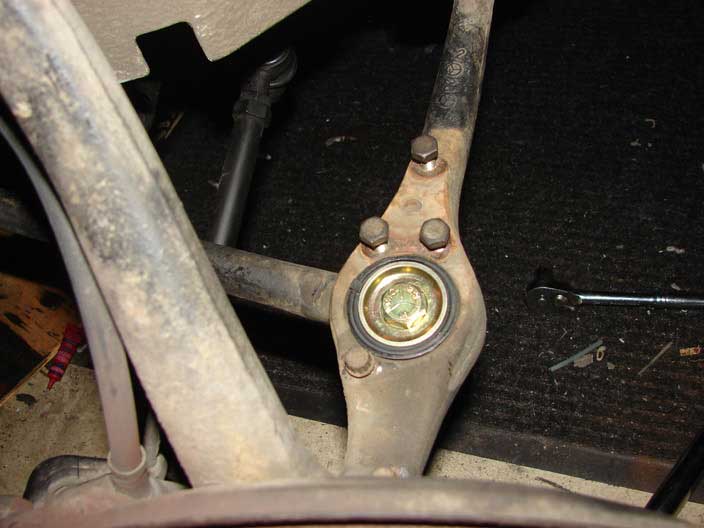
15) Bolt the guide rod mount to the body. Use blue threadlocker on the bolts and torque to 35 Nm. (Why does the blue stuff come in a red tube, and the red stuff come in a blue tube?!)
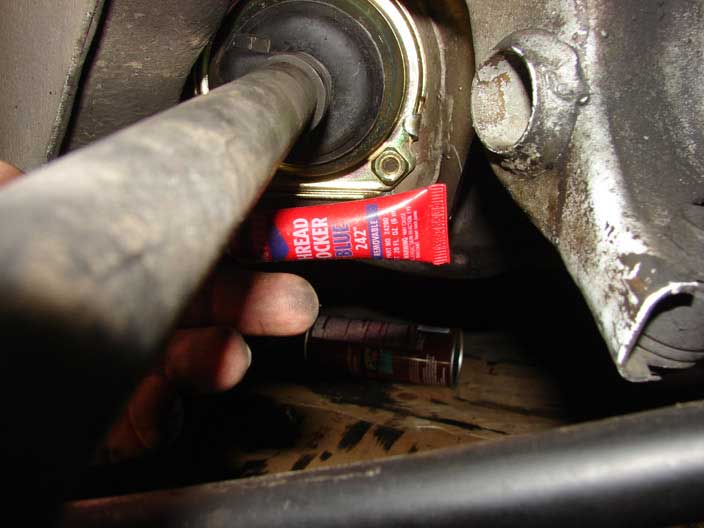
16) Reinstall the LCA. Use a rubber mallet to tap the LCA in to place, then reinsert the eccentric bolt in the same position you noted earlier. Snug the nut firmly, but do not torque until the car is back on the ground. The torque spec is 180 Nm.
17) Be sure that the front guide rod bushing is in place squarely and the notches in the rubber are pointed towards the back of the guide rod. Torque front mount bolt to 70 Nm (10mm bolt) or 105 Nm (12mm Bolt)
18) Remove bolt from the end of the sway bar and the nut on the upper ball joint, then pop the ball joint free of the steering knuckle. A $2 harbor freight pickle fork did the trick for me.
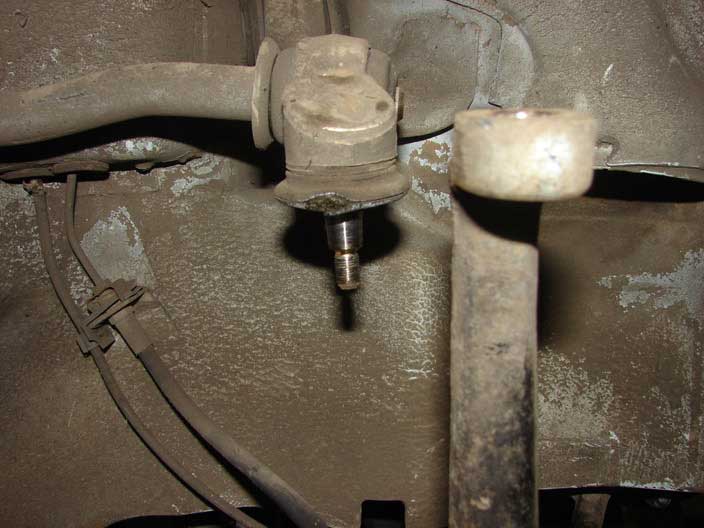
19) If you are planning to replace your lower ball joints remove the brake caliper and hang it from the car with a piece of wire (not the hose), remove the tie rod ball joint from the steering knuckle, remove the lower ball joint nut and remove the steering knuckle. Have the old ball joint pressed out and the new one pressed in and re-attach the steering knuckle. Torque the lower ball joint nut to 80 Nm, and the tie rod ball joint nut to 35 Nm. (I skipped this step because my lower ball joints were OK)
20) Remove the bolt from the inner mount of the upper control arm, twist the upper control arm towards the front of the car and remove it.
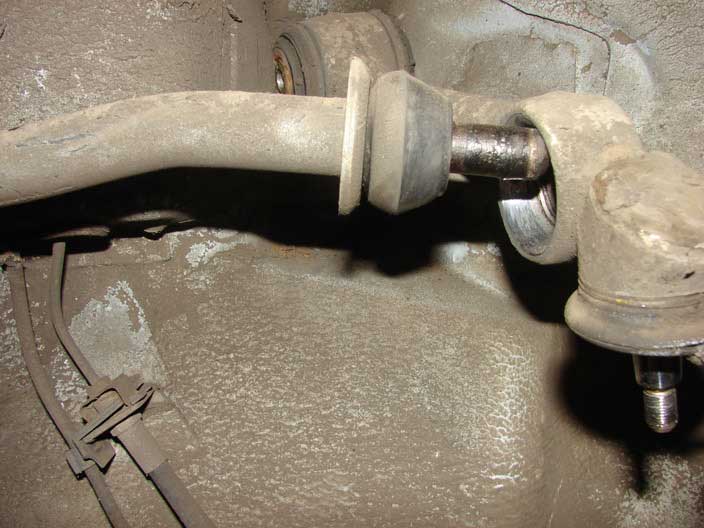
21) Clean the old rubber and rust off of the swaybar end and clean the dirt from the UCA pivot point.
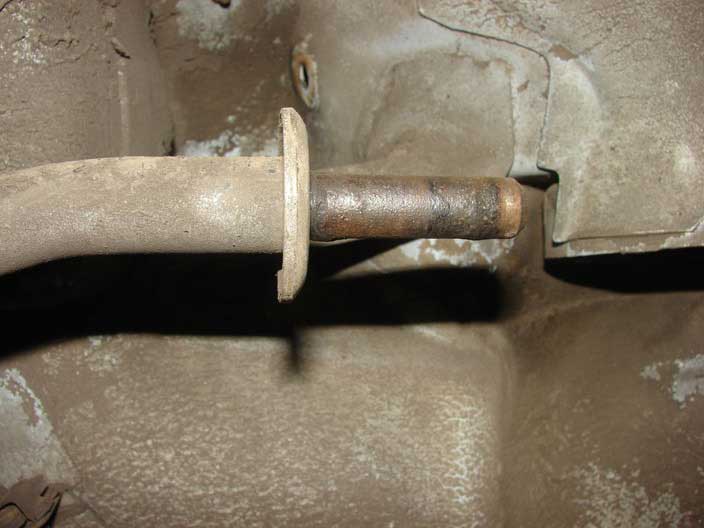

22) Make sure you have the correct UCA for the side of the car you are working on. Lightly grease the sides of the pivot point on the new UCA. Take car not to get grease on the rubber bushing.
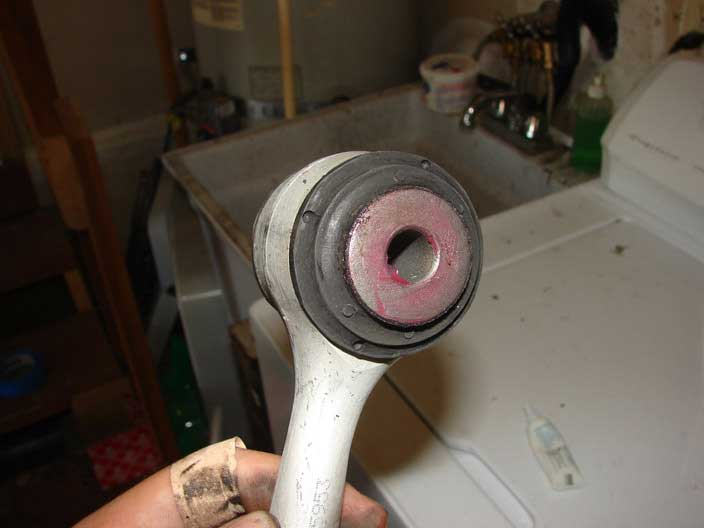
23) Install one of the rubber new sway bar mounts on the sway bar, then slip the UCA onto the sway bar end and use a rubber mallet to tap it into place. It will be much easier to get the new UCA in place if you have popped the opposite side’s upper ball joint free to relieve the torsion on the sway bar. A long 3/8†socket extension makes a good tool to help align the UCA pivot point with the holes in the body.
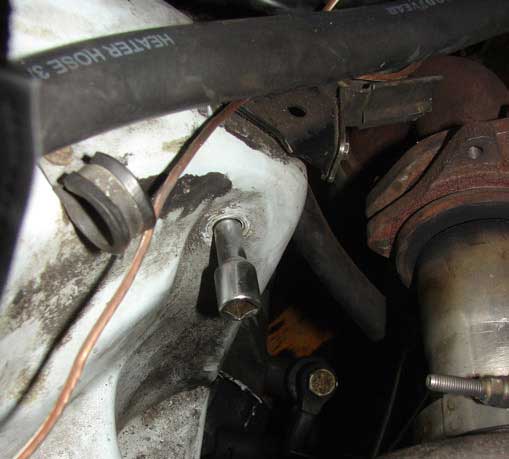
24) Lightly grease and install the bolt at the pivot point of the UCA and torque to 85 Nm. Install the other half of the sway bar bushing and install the bolt and two large, nesting washers into the end of the sway bar using blue threadlocker on the bolt threads. Torque bolt to 65 Nm.
25) Align the upper ball joint with the steering knuckle. Use a jack under the LCA to raise the steering knuckle in to place to prevent the ball joint from spinning when you tighten the nut. Torque the nut to 40 Nm.
26) It is probably a good idea to clean, remove the rust, and paint your spring perch. Reinstall the spring perch and shock absorber using blue threadlocker. Torque the lower shock bolts to 20 Nm and the spring perch bolts "gute’n tight" (say with a German accent)
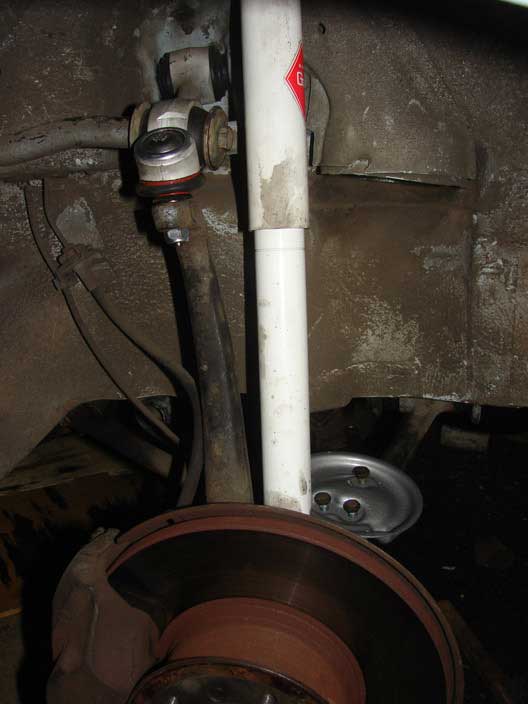
27) Reinstall the spring.

28) Re-install the wheel and lower the car to the ground. You will now need to have your car aligned by a shop that is familiar with older Mercedes. Don’t forget to re-torque all bolts and nuts after a day or two of driving.
Discuss this DIY here.
-bgkast
CategoryDiy