Broken Glow Plug Removal
on the OM606 OM605 OM604
by mcreynol
07/31/08
How to remove the dreaded sheared off glowplug
The OM60x series of 4 valve Mercedes diesels are notorious for seizing glow plugs. Apparently the plugs don't seat properly at the combustion chamber end. This allows carbon to get packed in around the barrel. Over time the plugs become glued into place. The narrow neck between the hex nut and the threaded shaft isn't up to the task of untwisting the plug and it snaps off. The problem has nothing to do with the threads sticking, though the aluminum steel combination can't be helping.
If you have a broken off glow plug, you are faced with a choice:
A: Remove the head and take it down to a machine shop to have the plug machined out
OR
B: Make a simple puller to yank out the plug.
This page describes how to do ( B )
Tools:
- vice grips
- drill motor
- 1cm drill bit (13/32" is just right, 7/16" might be too big)
- M6 x 1.0 Tap and drill set
- hardened M6 x 1.0 bolt, at least 6cm long
- hardened M6 nut
- assortment of washers
- a 13mm X 3/8" standard depth socket
- patience, this is an expensive head
1) Remove the hex head and center electrode.
Vice grips will do nicely. Just tear the off the hex part and then clamp onto the electrode and lever it out. The electrode is a good 4cm long and can be welded in there pretty well. It has to come out for the next steps.
2) Freeing the threads
Drill out the threaded portion of the plug. Use a 1cm/.4" drill bit to drill the first 15mm of the snapped off plug. This gets you through the threaded portion of the plug. Now the plug can be pulled straight out, rather than needing to be turned. If you drill straight along the axis of the plug you will leave the threads of the plug in the head. The head will be undamaged. Blow out the chips.
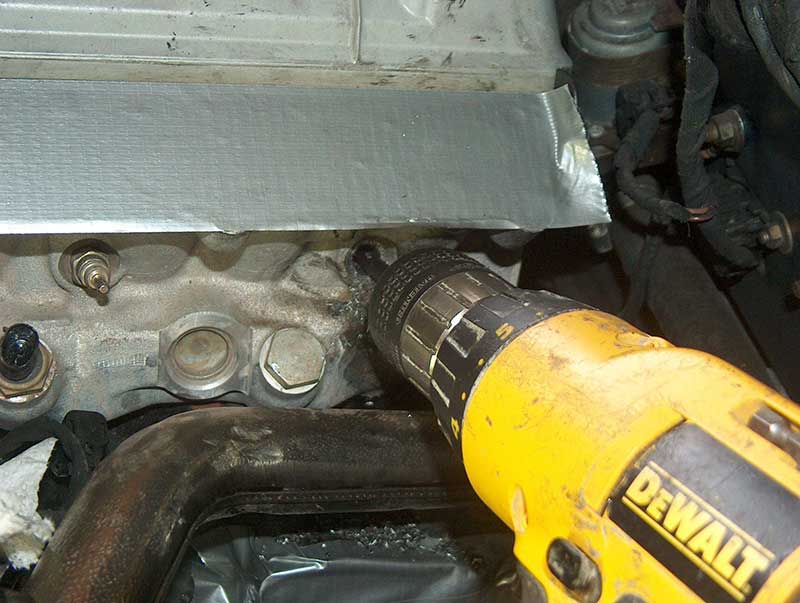
3) Drilling the body
Drill out the hollow part of the plug with the 5mm drill from the M6 Tap set. Go in at least 35mm and not more than 45mm, as measured from the surface of the head. Blow out the chips.
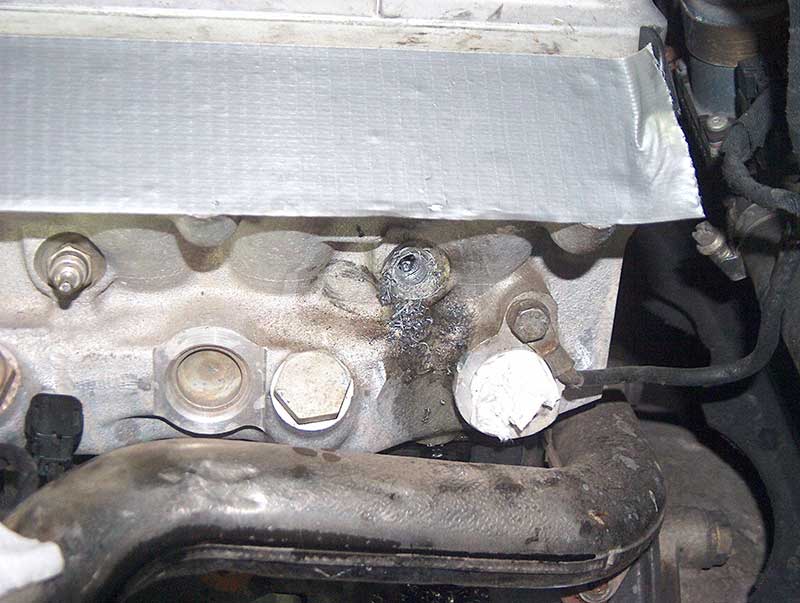
4) Tapping the body
Use a M6x1.0 tap to make threads on the inside of the glow plug body as far in as the tap will go smoothly. Whatever you do, don't break the tap in there. Take your time. Blow out the chips. (picture shows larger tap, use a M6 for this step)
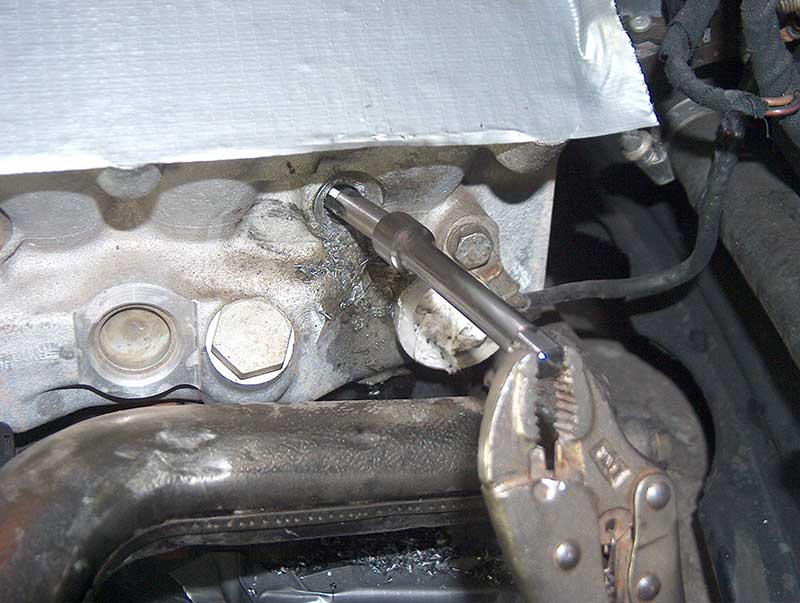
5) Building the puller
Thread the M6 nut onto the M6 bolt. Then stack some washers on to the bolt and thread it as far as it can go into the (now threaded) glow plug. Just get it snug, no real force is required.
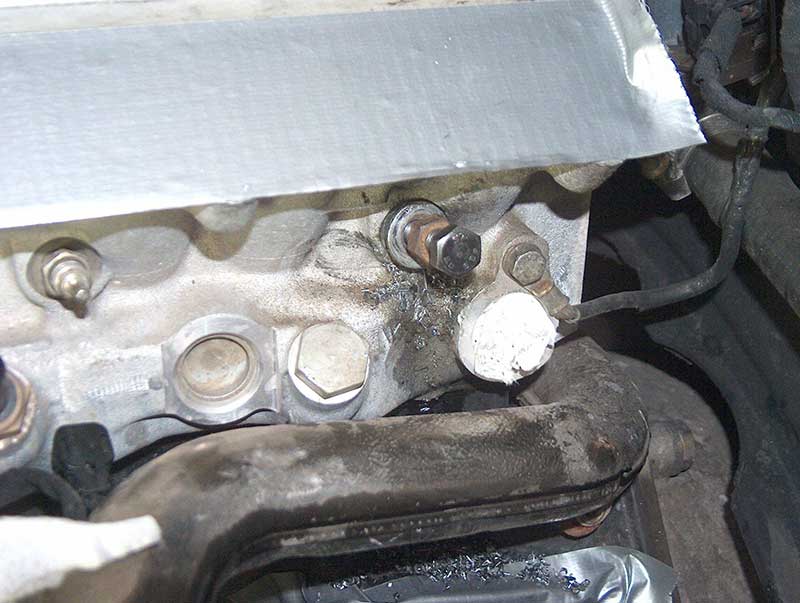
6) Pull the plug
Turn the nut clockwise so that it gets further away from the bolt head. This will force the plug out of the head. The first real resistance will be firm. After the grip of the carbon gunk is broken it will move easier. Then it will stop moving. This means that the plug is jammed up against the washers. Unscrew the puller and pry out any bits (thread rings, etc) that are easily removable.
Reassemble the puller with a 13mm x 3/8" socket instead of the washers. The hollow formed by the socket will allow the plug to move further out of the head.
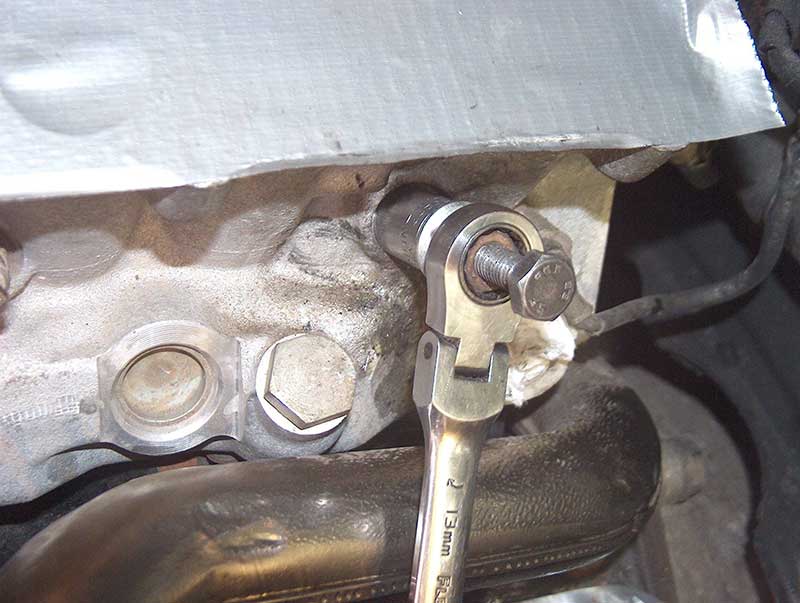
7) Success!
When the bolt head starts to turn, you will have pulled the plug out far enough that you can yank it out by hand. This is what you should see:
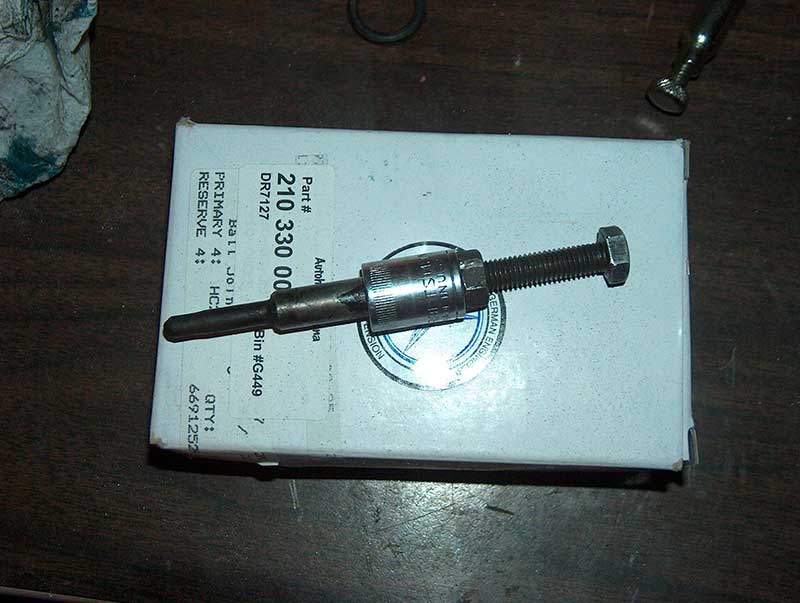
8) Cleanup
Suction out the chips. Then, insert some wadded up tissue paper into the hole. Now you can clean up or repair the threads. If you were careful the threads should be good and you can install a new plug. If the threads are damaged, install a Time-Sert or Heli-coil (M12x1.25 x 15mm). Remember to ream out the glow plug hole (Klann KL-0369-13)
9) End result
As an experiment, I've chosen to coat the entire body of the plug with Hylomar HPF. Aside from sealing the nose and threads this sealant is fairly temperature stable and may fill up the space that would otherwise fill up with carbon. We'll see in 50Kmiles or so.

Discuss this DIY here.
-mcreynol
CategoryDiy