Self Leveling Suspension Valve Rebuild
on the 1984 300TD Turbo (W123)
by Douglas.Sherida
08/01/07
DIY: Rebuild the self leveling suspension SLS valve on w123 300TD wagon sagging rear
First let me apologize for the overly long thread title. I wanted to make it amenable to searching the archives.
This post is meant purely as a DIY. Time to give back to the forum.
The car:
1984 euro 300TD turbo, but I think this will apply to most w123 wagons with self leveling suspension (SLS).
Problem:
The car rides fine, not too bouncy or bone jarringly stiff *. When the engine is running the car sits level, but after being parked for a few hours the rear end of the wagon sags down a bit. Its most noticeable because in the morning when the car is started you can feel the back end up the car raise up. The SLS valve (figure 1) is wet with hydraulic oil. The SLS actuators (rear struts) are NOT leaking (they are dry).
Causes:
1) One or more of the o-rings in the SLS valve is leaking and
2) the rear coil springs are either worn or broken and should be replaced (or possibly shimmed if it doesn't sag too much), and/or
3) the SLS ride height is adjusted too high. In my case all three are true, but if you can feel your car raise up when it is started at least two of the above are true (unless you just loaded it down with about 400 lbs).
If the car has good springs, the unloaded car won't sag even if the SLS is disconnected.
Fix:
1) Rebuild (replace the o-rings in) the SLS valve.
2) Replace the rear springs (beyond the scope of this thread).
3) Adjust the ride height.
Rebuilding the SLS valve:
Tools required:
- Jack and (2) jack stands or (2) ramps
- (2) 17 mm wrenches
- 12 mm open end wrench
- 11 mm open end wrench
- (2) 10 mm wrenches (one open end)
- 8 mm allen key
- Small bent pick (dental pick) or very sharp forceps)
- 1 foot piece of 1/4" ID hose
- Clean dry plastic bottle
- Drain pan
Parts Required:
metric o-rings (buna-nitrile or viton) dimensions are listed in mm as cross section (CS) x internal diameter (ID)
- (1) 2 x 58
- (2) 2 x 7
- (1) 1.6 x 10.1
- (1) 1.6 x 7.1 (see below for availability)
- 1 liter of MB hydraulic oil (to replace lost fluid, available through FastLane) the total capacity of the SLS system is 3.5 liters
Time required:
2-3 hrs
Difficulty:
No more difficult than adjusting the valves
1) Chock the front wheels securely and jack up the back end of the car just enough to get under it. Place jack stands under the trailing arms and carefully lower the car. Make sure that the car is secure before you climb under it. Alternatively, back it up onto ramps, then chock the front wheels. The idea here is that the rear suspension should be compressed before you open the hydraulic system and release the pressure, this will minimize the amount of hydraulic fluid lost. (If your springs aren't too bad and you don't eat too much you may be able to do the entire job without jacking up the car.) Ideally, the suspension should be compressed and the car should be sitting level (If you had good springs you could do this).
2) Disconnect the SLS height adjusting rod (figure 1.A, looks like a throttle linkage rod) from the valve lever arm (figure 1.B). Use the open end 10 mm wrench to hold the ball stud and another 10 mm wrench to undo the nut. (The picture for figure 1 was taken with the car jacked up and the wheels hanging, that is why the lever arm is pointing down from "normal".)
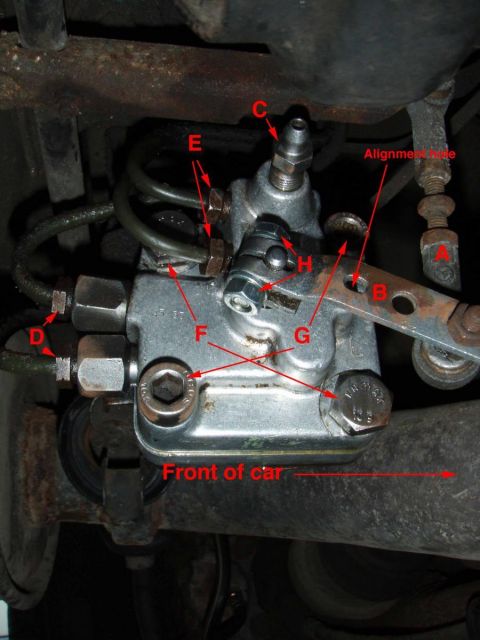
3) Start the car and crawl back under it. VERY CAREFULLY release the pressure on the SLS actuators by rotating the SLS valve lever clockwise (CW) about 10 degrees. WARNING: The rear end of the car will come down to its lowest point (resting on the springs), and if your springs are really bad it may squish you. My springs weren't too bad and I could do this with the car on the ground, so I had fun playing with the valve lever for a while (car goes up, car goes down, car goes up, car goes down, etc.). Don't let the car raise too far. I don't know that anything bad will happen, but it seems like a bad idea to overextend the actuators. Turn the car off.
4) Attach a hose to the bleeder valve on the SLS valve (figure 1.C) and put the other end in the bottle. Loosen the bleeder valve (11 mm ? open end wrench) to drain any residual pressure in the SLS system.
5) Place the drain pan under the valve. Disconnect the hydraulic oil feed and return lines from the valve (figure 1.D, 12 mm open end wrench). They may leak oil when loosened, but it should stop in a minute.
6) Disconnect the hydraulic lines to the actuators from the valve (figure 1.E), 11 mm open end wrench). They may leak oil when loosened, but it should stop in a minute.
7) Remove the two bolts holding the SLS valve to the bracket (figure 1.F, two 17 mm wrenches).
Take the valve to a clean work area. Before you disassemble the valve, note the relative orientation of the two halves (honestly I don't think it matters, but hey better safe than sorry). My valve was marked 115- 328-0521. Also, when you separate the two halves of the valve there is a piston with two springs in it that may fly apart, so proceed cautiously.
8) Remove the two bolts holding the two halves of the valve together (figure 1.G, 8 mm allen key and 17 mm wrench). Beware of small flying parts. Note the orientation of the cam inside the valve (figure 2.A), the lobe of the cam points away from the valve lever arm (toward the hydraulic line fittings toward back of the car). Replace the 2 x 58 o-ring (figure 2.B). In figure 2 the o-ring is stuck to main valve body, it should be in the recessed channel on the other half (figure 2.C). This is probably the o-ring that was leaking, but since its out and apart you might as well replace the rest of the o-rings.
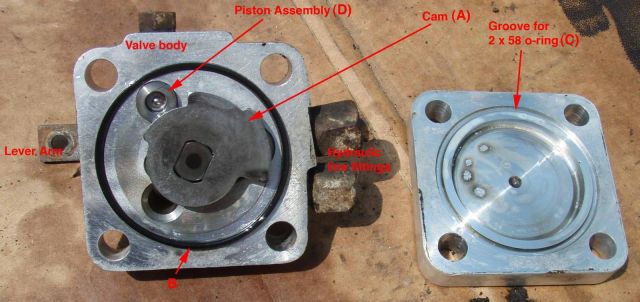
9) If it didn't come flying apart when you separated the valve, pull the cam off of the lever arm shaft. Carefully remove the piston (figure 2.D) without scratching it. I used a pair of needle nose pliers and some cotton cloth to prevent scratching the piston. The piston assembly is actually 2 pistons (outer and inner), 2 springs and a ball bearing (figure 3). There is a second larger ball bearing trapped in a passage in the valve body behind the piston. I didn't measure any of these parts so I can't help you order replacements, so don't lose them.
10) Remove the bolt holding the valve lever arm to the shaft (figure 1.H, 10 mm wrenches). Pull the valve lever arm off of the shaft. Push the shaft out through the valve body. Use the bent pick to remove and replace the two o-rings from the valve body (2 x 7) where they seal against the shaft. Re-install the shaft, lever arm and 10 mm bolt.
11) Use the bent pick to remove and replace the outer (1.6 x 10.1) and inner (1.6 x 7.1) o-rings on the outer piston.
Reassemble the piston as follows (figure 3):
- drop the larger ball bearing into the passage in the valve body behind the piston letting it fall toward the center of the valve (not pictured),
- slide the larger spring over the inner piston,
- slide the inner piston (and spring) into the outer piston,
- insert the smaller ball bearing into the inner piston from the bottom,
- insert the smaller spring into the inner piston from the bottom,
- insert the piston assembly back into the valve body.
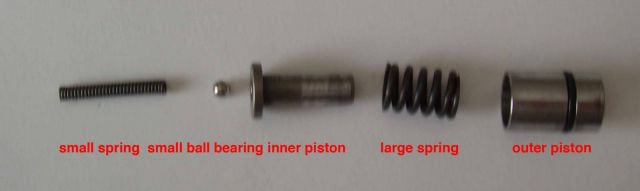
12) Rotate the valve lever arm to its correct position (away from the hydraulic line fittings). There are corresponding holes on the lever arm and the valve body that line up when it is in the correct position. Re-install the cam on the lever arm shaft with the biggest lobe pointing away from the valve lever arm and the smaller lobes pointing toward the top of the valve (figure 2.A).
13) Reassemble the two halves of the valve in the original orientation. Re-install the two bolts that hold it together (figure 1.G). Note that one of these bolts is longer than the rest as the valve body is thicker in one corner.
14) Reinstall the valve on it bracket and reconnect the hydraulic lines.
15) Check the level of fluid in the hydraulic resevoir (I only lost about 250 mL), it doesn't need to be full just so long as it won't run the pump dry. Start the car. Play with the valve lever arm again (car goes up, car goes down, car goes up, car goes down, etc.). The car should raise when you turn the lever about 10 degrees CCW from horizontal and lower at about 10 degrees CW from horizontal). If it requires large rotation of the lever to raise and lower the car, you may have installed the cam in the wrong orientation.
16) Use the lever arm to adjust the ride height where you want it and return the lever arm to its "normal" position (when the hole in the arm and the hole in the valve body line up). If your car rode at the proper height before, you can just reconnect the adjusting arm (and order new rear springs). The PO had adjusted mine to ride too high. The adjusting rod can be lengthened (to make it ride lower) or shortened (to make it ride higher), by loosening the 10 mm locknuts on the center shaft at the sockets and the center shaft turning the center shaft by the 10 mm fitting in the middle. Retighten the lock nuts and you're done. (The picture for figure 1 was taken with the car jacked up and the wheels hanging, that is why the lever arm is pointing down from "normal".)
- Poor ride quality in the rear is often an indicator of bad accumulators.
- I was informed by FastLane that the original MB rebuild kit for this valve is no longer available. I purchased the small o-rings from McMaster-Carr and the large o-ring from Marco Rubber. Unfortunately, you cannot buy just one o-ring, so I ended up with enough to rebuild 20 valves. It cost me just over $75. If you need to rebuild your own valve, I'd be very happy to send you 2 complete sets of o-rings for $10 (shipped). I hope this isn't viewed as solicitation, I'm just trying to help out (and maybe break even).
EDIT 01-03-08: I broke even and ran out of the large o-rings. Contact Andrew at Biodiesel300TD for o-ring kits.
- A word about proper ride height: The unloaded curb weight of the car should be carried entirely by the springs (i.e. If the car has good springs, the unloaded car won't sag even if the SLS is disconnected). I keep repeating this because its important. The fix I describe in this thread is only part of the job (the easy part), and if you don't replace the springs (or shim them) you will likely have to repeat the job all too soon (or worse, prematurely wear out the actuators). When the SLS system is working properly you should never know its there until you put a heavy load in the rear cargo area with the engine off. This is the only time you should see the car level itself on start up.
Someone recently posted a great blue print style mechanical drawing of a w123 sedan that shows measurements for the stock ride height (though there may be differences between euro and US specs), but I can't find the thread right now.
Big thanks to whunter, who suggested that when I do the repair I document it so I could write this DIY.
Discuss this DIY here.
-Douglas.Sherida
CategoryDiy